Software for Continuous Casting
Dynamic control of secondary cooling and roll gap for continuous casting
CC-COOL N GAP was developed to control secondary cooling water flow and roll gap dynamically for continuous casting based on predefined surface temperature profile. Dynamic secondary cooling and roll gap control is very useful for obtaining good qualities of strand consistently. CC-COOL N GAP can be used for on-line control and off-line simulation of secondary cooling and roll gap. Target surface temperature profiles included CC-COOL N GAP are optimized for minimizing internal/surface crack of strand.
Features
Using on-line thermal tracking model (based on Finite Element Method)Using actual casting conditions (casting speed, cooling water flows)
Tunable model by user (provide open parameters for tuning of thermal model)
Using both dynamic mode (target temperature base) and semi-dynamic mode (cooling water flow base)
Using on/off margin control logic (modifying water flow by width of strand)
Using movable spray margin control logic (modifying water flow by nozzle height determined by corner margin length)
Tracking of steel grade, strand width, and cooling pattern
Using PID control for maintaining surface temperature
Using stabilizing logic for minimizing fluctuation of water flow (in case of casting start)
Coupled with dynamic control of strand gap for soft reduction
Supplying dynamic and semi-dynamic cooling pattern obtained by process optimization based on qualities(internal/surface crack) of strand
Flexible GUI (Customizing operating and monitoring GUI by user’s convenience)
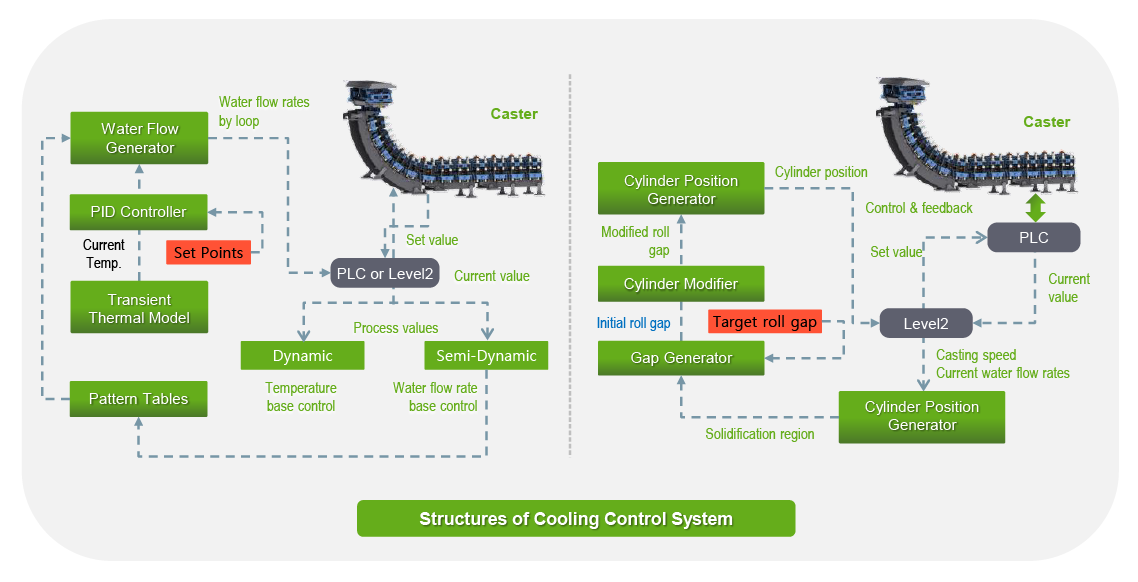
Simulation System
Set up and off-line simulation at any PCSet up machine specifications (roll geometry, cooling zone, loop, segment information, etc)
Set up several patterns (cooling patterns, trigger points, margin patterns, roll gap patterns, etc)
Transmission of set up data to on-line control system
Same functionality with on-line system
Dynamic simulation for checking patterns in order to optimizing qualities
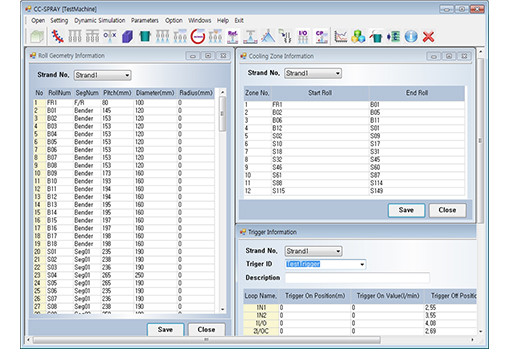
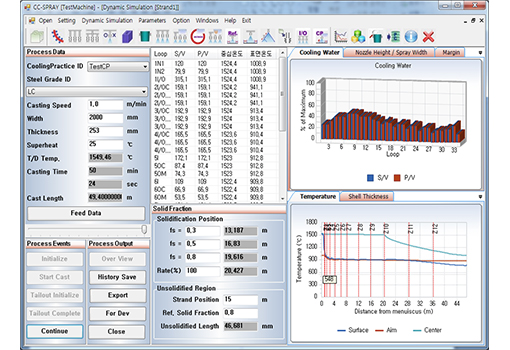
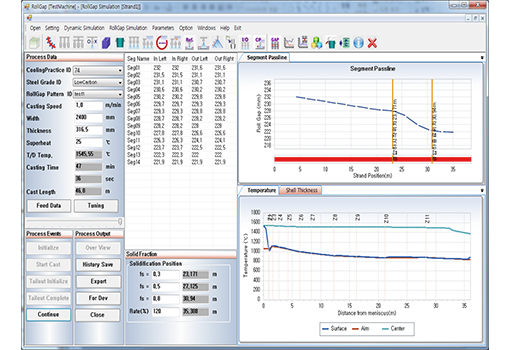
Cooling / Roll Gap Pattern
Grouping steel grade by carbon and special alloy contents within product mixCooling pattern based on target temperature for dynamic mode
Cooling pattern based on water flow rate for semi-dynamic mode
Optimizing cooling pattern by steel grade group with process optimizing simulation (using CC-MASTER, not included in CC-COOL N GAP)
Margin pattern based on surface corner temperature profile preventing corner over cooling
I/O weight pattern preventing strand thermal bending after final roll position
Roll gap pattern for soft reduction
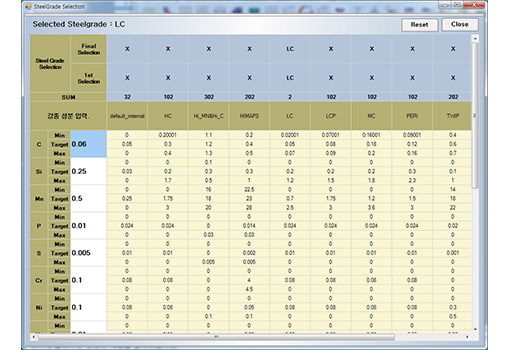

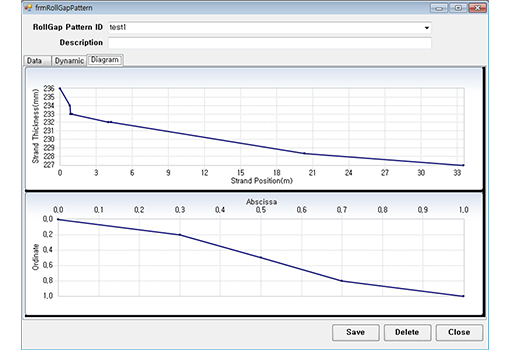
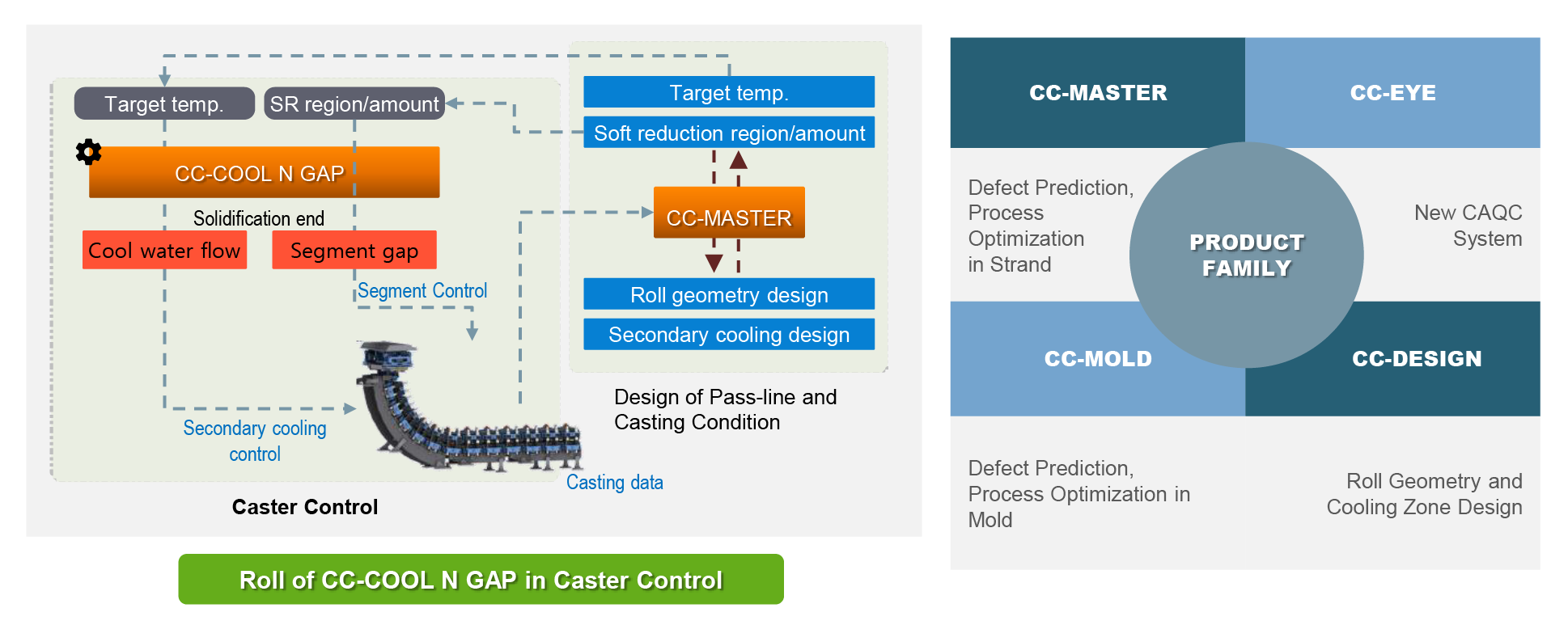
Advanced simulating
Software for Continuous Casting
CC-COOL N GAP
Catalog Download
Dynamic control of secondary cooling and roll gap for continuous casting
CC-COOL N GAP was developed to control secondary cooling water flow and roll gap dynamically for continuous casting based on predefined surface temperature profile. Dynamic secondary cooling and roll gap control is very useful for obtaining good qualities of strand consistently. CC-COOL N GAP can be used for on-line control and off-line simulation of secondary cooling and roll gap. Target surface temperature profiles included in CC-COOL N GAP are optimized for minimizing internal/surface crack of strand.
Features
Using on-line thermal tracking model (based on Finite Element Method)Using actual casting conditions (casting speed, cooling water flows)
Tunable model by user (provide open parameters for tuning of thermal model)
Using both dynamic mode (target temperature base) and semi-dynamic mode (cooling water flow base)
Using on/off margin control logic (modifying water flow by width of strand)
Using movable spray margin control logic (modifying water flow by nozzle height determined by corner margin length)
Tracking of steel grade, strand width, and cooling pattern
Using PID control for maintaining surface temperature
Using stabilizing logic for minimizing fluctuation of water flow (in case of casting start)
Coupled with dynamic control of strand gap for soft reduction
Supplying dynamic and semi-dynamic cooling pattern obtained by process optimization based on qualities(internal/surface crack) of strand
Flexible GUI (Customizing operating and monitoring GUI by user’s convenience)
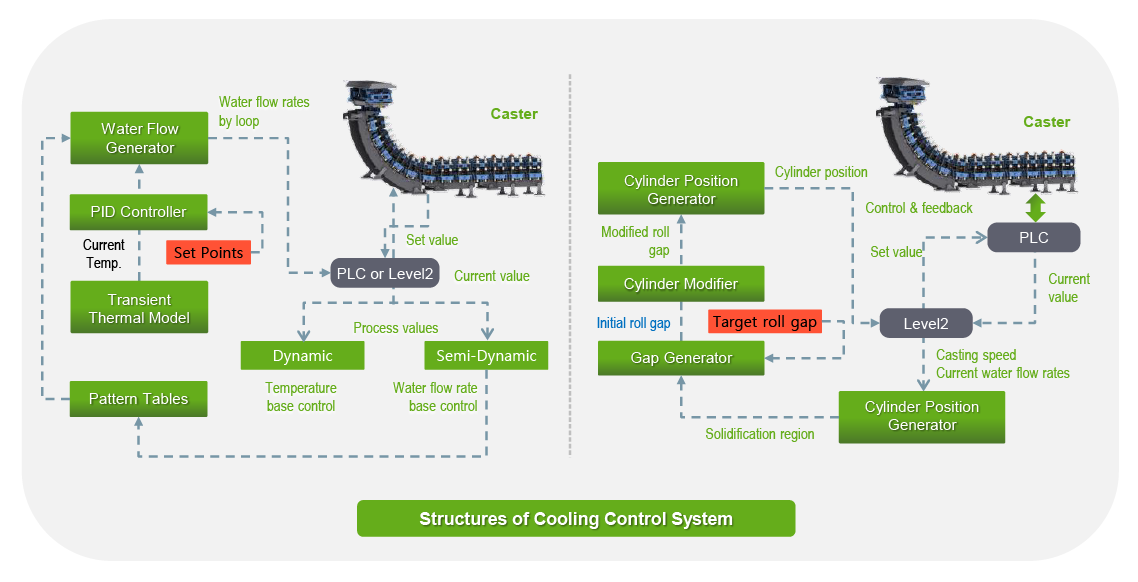
Simulation System
Set up and off-line simulation at any PCSet up machine specifications (roll geometry, cooling zone, loop, segment information, etc)
Set up several patterns (cooling patterns, trigger points, margin patterns, roll gap patterns, etc)
Transmission of set up data to on-line control system
Same functionality with on-line system
Dynamic simulation for checking patterns in order to optimizing qualities
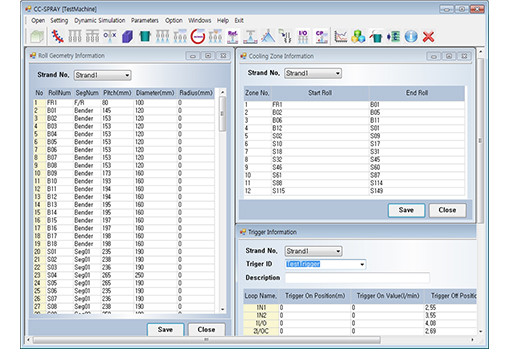
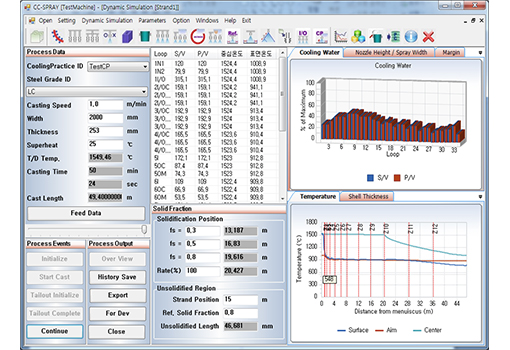
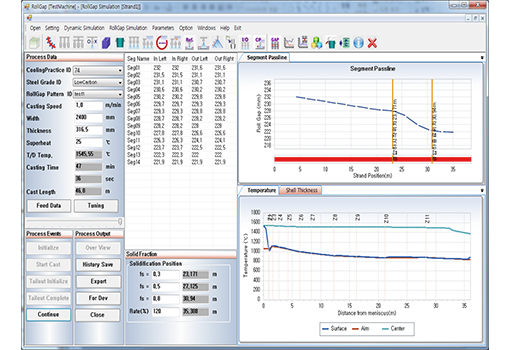
Cooling / Roll Gap Pattern
Grouping steel grade by carbon and special alloy contents within product mixCooling pattern based on target temperature for dynamic mode
Cooling pattern based on water flow rate for semi-dynamic mode
Optimizing cooling pattern by steel grade group with process optimizing simulation (using CC-MASTER, not included in CC-COOL N GAP)
Margin pattern based on surface corner temperature profile preventing corner over cooling
I/O weight pattern preventing strand thermal bending after final roll position
Roll gap pattern for soft reduction
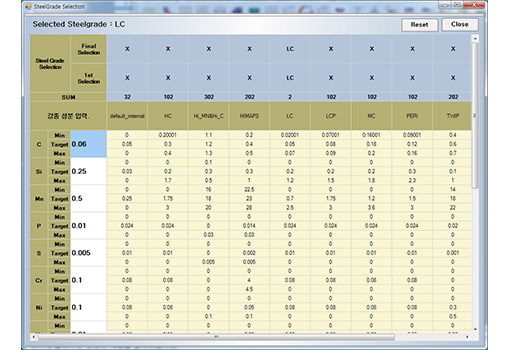

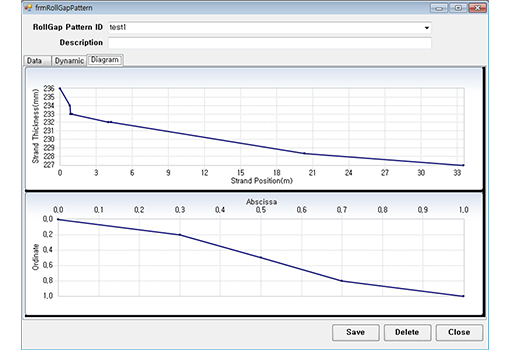
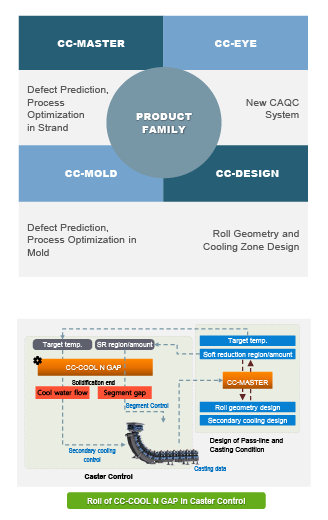